In the whole process of measuring the angle and inclination of goods, there are often repeated precision differences. One person uses the same method but the deviation is 0.6 degrees.
In the mobile phone software of many image measuring instruments, the parallel line collection is set to two points by default. For regular and parallel linear parts, it is not easy to cause large deviations in angle measurement, but it is not very good for parallel linear. For parts with many burrs, the way of collecting parallel lines at two points produces large deviations, and the repeat accuracy is also poor. The angle formed by such parallel lines, the repeatability of several measurements, is undoubtedly not ideal.
If we use more regression lines to clear both sides of the angle, the personal input parallel line is closer to the measured steel frame line, then the error will be reduced, in addition, the measurement deviation will be greatly reduced, and the repeatability will be greatly improved.
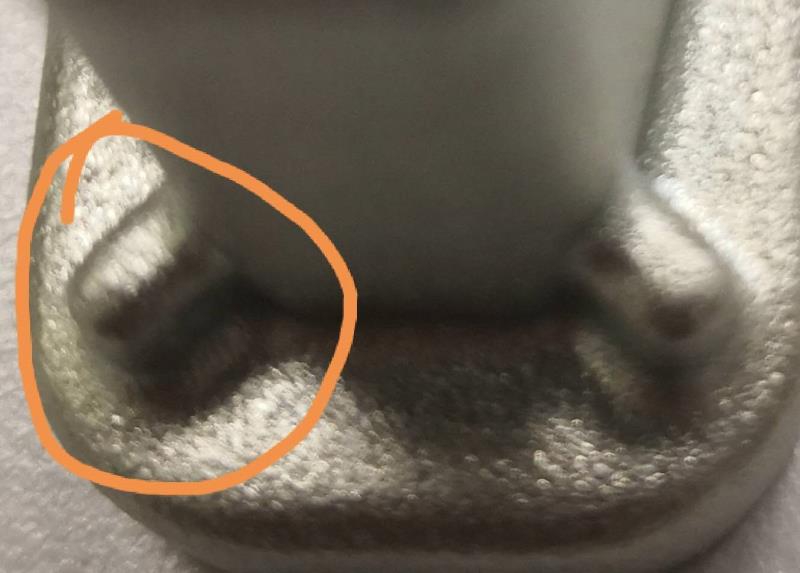
Due to the limited display on the screen, the magnification of the image detection instrument is large (usually 28x-180 times in 0.7-4.5 files). Some steel specifications displayed on the screen are only millimeters, and many precise surveyors subconsciously display only some collection points and line initials on the screen of the test plan. If there are errors in the collected points and the fewer line segments are collected, the measured angle value error will be greater, and the longer the line segment, the smaller the measured angle value error will be. The angle of the basic knowledge is 30 degrees, the error of the collection point is 0.25mm, and the length of the damaged line is measured accurately and accurately.
Therefore, in the case of measuring the angle, we should collect the lines on both sides of the angle as long as possible. If the display area on the screen is small, we can move the console, pick a point at the starting point of the parallel line to which the angle belongs, and then at the end point. Take a point at the station, so that the angle deviation of the measurement may be greatly reduced.
For many mechanical parts, the measured angle boundary is very short, only 3 mm ~ 2 mm, such as the rounded corners of shaft parts. If we also use the camera lens with a minimum of 0.7, or 1 to measure the point, the steel parts can only be displayed from 48mm to 12b250m. The error of the point of picking will cause a great harm to the measured value. If we switch to a larger magnification of 3 or 4, the steel parts can be displayed from 24b250m to 48b250m, the specific conditions of the image edge are more easily observed, and the sampling error may be minimized. However, this type of method also causes a lot of trouble. The graphics are too large, and the display information dialog box only displays a small part of the information. However, for skilled inspection staff who are practically operating and pursuing perfect high-precision quality inspection, this should None is a problem.